Idaho State University interns design robot for nuclear fuel facility
July 6, 2016
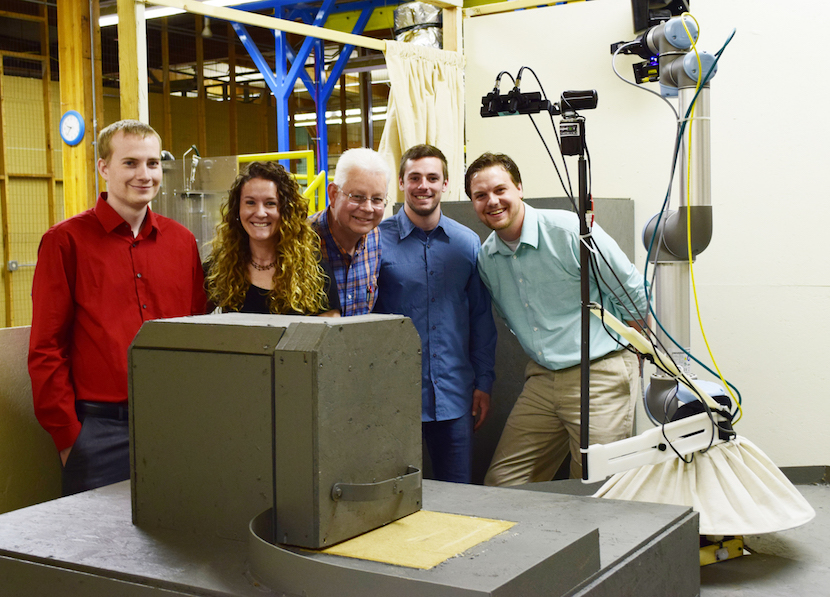
By Nora Heikkinen, INL Public Affairs and Strategic Initiatives
Cheers erupted from an audience peering over plywood walls into a mock-up work cell. The robot inside had successfully transported a surrogate radioactive sample from an inter-facility transfer box, out of its transfer containers, into an examination instrument, and then back again. It was a satisfying ending to a nine-month-long project for four Idaho State University (ISU) mechanical and nuclear engineering students serving internships at Idaho National Laboratory.
One of those students, Larinda Nichols, served a prior INL internship, which included attending design meetings for future post-irradiation examination (PIE) work. From that, Mitchell Meyer, the lab’s director of characterization and advanced PIE, assigned Nichols a senior project to demonstrate the use of robotics in instrument cells.
Nichols formed a team with fellow students Cody Race, Jerron Berrett and Sage Thibodeau. They received approval from ISU and – with the help of INL mentor Kevin Croft, a senior advisory engineer in INL’s Environmental Engineering & Technology Department – began work on the project.
The students set out to design a robotic system to be used as a demonstration project for INL engineers. If the students’ feasibility study was successful, lab engineers could design a similar system to handle radioactive materials for PIE at INL’s Materials and Fuels Complex (MFC).
The mock-up cell and robot needed to mimic what a robotic system would require. The robot must remotely load and unload radioactive samples from the inter-facility transport system (called ‘pneumatic’ and works much like a bank drive-through) and its layered containers, load the sample into a micro-/nanoscale examination instrument, such as a focused ion beam (including opening and closing its loading drawer), and then reverse the process. The system is required to be accurate within a 0.01-inch radius from the target location 99.99 percent of the time. Also, based on the characteristics of the potential samples, the equipment needs to operate within a radiation environment of approximately one curie of Cobalt-60. Any materials being examined will be less than this level of energy, and equipment must be able to reliably withstand operation under these conditions without significant damage. The interns ensured their robot and mock-up area complied with all of these requirements.
The group researched nontraditional remote handling equipment. A trade study led it to choose a commercial robot based upon program requirements and objectives. The team also explored the use of vision technologies, which would take the place of the shield windows typically used in hot cell facilities. INL provided the equipment needed for demonstrating both whole-area viewing and a 3-D vision system for close-up viewing of work.
“This team went above and beyond expectations,” said Croft. “It was a great pleasure working with such intellectually voracious people. They are amazing.”
After much research and trial and error, the team built the mock-up robotic work cell. The key piece of equipment is the commercial 6-axis robot (plus gripper), with each joint having 360 degrees of motion. The team programmed the robot to complete all the necessary moves of the sample, returning it safely into the mock-up pneumatic transfer box. This robotic process is supported by an attached machine vision system for object identification, location and pickup. The robot is capable of retrieving a dropped sample using additional tools and teleoperations using video monitoring screens (much like a video game).
This setup is a “departure from traditional radioactive material handling,” Croft said. Because of the uniqueness of the planned facility, lack of radioactive contamination, and remote handling processes, workers will be able to complete maintenance and repairs without exposure to radiation. Master-slave manipulators and shielded windows work well for the nuclear industry, however, they are expensive to design, purchase, install and maintain. Using robotics potentially saves money and provides a friendlier work environment for operators.
“It’s evident that we don’t have the budgets we used to, but equipment and fabrication costs continue to increase,” Croft said.
The costs of the robots and vision systems are anticipated to be much less than those of current technologies. Development work by INL engineers, however, is still required to create equipment that is radiation resistant, sufficiently flexible, and robust to operate well inside the environments of typical hot cells.
The project was funded by INL, which was appreciated by the interns.
“This was an amazing experience,” Nichols said.
Group intern projects are one way INL works with students to enhance science, technology, engineering and math (STEM) education and build a talent pipeline for the next generation of INL employees. INL supports college internships, joint appointments, postdoctoral appointments, academic visitors, and international researcher exchanges, interactions that benefit both the laboratory and the universities.
“The project results demonstrated that the direction we’re going is doable,” Croft said. “Like any alternative to traditional processes, however, it needs some additional development and vetting.”
Future work includes definitive ergonomic and economic analyses of the proposed technologies, as well as investigation and design of more tools and sensors. With a successful robotic demonstration to start, projects continuing this line of research – whether completed by interns or INL staff – hint at an exciting future.
Here is a link to a video on the project: https://youtu.be/xghZkXgvdqU. Video courtesy of Chris Morgan, INL
Link to feature on INL.gov: https://www.inl.gov/article/
Photo information (Photos courtesy of INL):
Top photo:
The intern team with their robot (to the right) inside of the mock-up cell. Left to right: Jerron Barrett, Larinda Nichols, mentor Kevin Croft, Sage Thibodeau and Cody Race.
Second photo:
Sage Thibodeau with the remote viewing monitors and robot control touchpad which allow manual operation of the robot from outside of the cell.
Third photo
The robot removed the sample from the clear transfer box, out of the two white sample containers, and transported it to the mock-up examination instrument.